I worked on finishing construction of the Magpie most of the day Saturday. This basically got the airframe to the point where all parts are ready to be covered. This includes the Sport Wing that is staying one step behind the slow flyer wing.
Sport Wing
I used a different technique for applying the strapping tape to the sport wing that worked well. Join the wing as before (I used 5 min epoxy this time). Next split the wing cradles at the front into a top and bottom halves. Take some 150 grit paper on a sanding block and sand down the ‘speed bumps’ that remain on the wing cradles from where the groove is cut into the wing for the strapping tape. Cut both pieces of the strapping tape and apply them to HALF the wing, top and bottom. tape the ends down if necessary. Wrap the wing in a length of parchment paper to prevent it sticking to the cradles. Put the wing in the cradle and weigh it down. Don’t be afraid to use lots of weight, I used a sheet pan to help spread the weight out evenly. Wait for the glue to cure and then repeat on the other half of the wing.
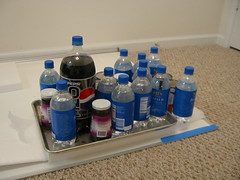
Empenage
For the empenage (thats the tail feathers) I stuck to the directions for the most part. The dowel that came with the kit was a bit bent so I swapped it for a carbon fibre rod of the same diameter. For the rudder and vertical stab I beveled the edges into a point. For the horizontal stab/elevator I used a single bevel as suggested in the instructions. Make sure you use a fresh blade for making the bevel cuts. Cut against a straight edge with the knife pointed ‘in’ towards you.
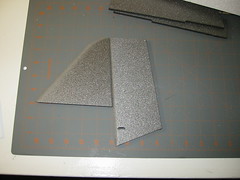
Fuselage
I added the wing saddles and servo plates to the fuselage. I moved the servo mounts about 3 inches forward of the location given in the instructions. This was something of a judgement call. Most people on RC Groups note that the model comes out tail heave. Also I would have needed servo extensions (an item missing from the required parts list!) to put the servos that far back. Whenever you move a servo further from the control surface you increase the amount of flex in the pushrods. To counter this you need to stiffen them or add guides. The elevator pushrod travels far from the fuselage so guides would need to be pretty big. I’m leaning towards using bigger diameter carbon fibre rods instead.
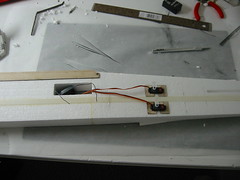
The manual calls for applying some thin plywood planks to the top-center of the wing. These take the load of the rubber bands and stop them from being crushed. I replaced this with some extra strapping tape that I bent to fit around the leading and trailing edges. I’m not sure how this will work out, they may be too narrow.
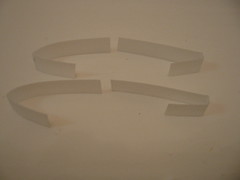
Working with 5 Minute Epoxy
I did all the assembly work with generic, hardware store, 5 Minute Epoxy. Here’s some suggestions if you’ve never worked with epoxy or never worked with epoxy that sets this fast:
- Work with a kitchen timer. Set it for 5 minutes and start the countdown before you start mixing.
- Mix vigorously for 30 seconds.
- Buy a bag of cheap Popsicle sticks for mixers/applicators. Try the crafts section or a crafts store.
- Apply as little epoxy as possible, scrape off any excess. Epoxy is heavy and it won’t penetrate.
- At 2 minutes to go do not apply any more epoxy from this batch to the work, its too late.
- At 1 minute to go clean any epoxy off your hands with rubbing alcohol.
- Finally as always, do a test bond before you do the first piece of your airplane.
For jobs bigger than a couple of square inches (like wing strapping) I would go with a 30 minute epoxy so you have more time to get things in position.
Covering with ‘Wing’ Tape
‘Wing’ Tape is actually Acrylic packing tape. Its thin, light, sticky and very frustrating to work with. You don’t really get a chance to reposition this stuff if you put it down wrong. I actually broke off part of the rear fuselage trying to reposition some tape. It doesn’t do compound curves well. You have to make lots of small cuts.
I did the fuselage first and it took nearly 3 hours. By the time I was don’t the adhesive spray was starting to loose its tackiness. I don’t want to do that again so I’m trying something different on the wings. I basically stopped working on the model on Sunday because I didn’t want to mess with the tape anymore.
Battery & Charger
The battery and charger showed up today. I chose, a Thunder Power Pro-Lite 2100mah 3S pack that weighs in at 5oz. the ’3S’ part means thats its 3 cells in series, this is also written as 3S-1P to denote that its one bank of series cells with no other bank in parallel. 3S-2P would be 2 banks of 3 cells in series, joined in parallel, confused yet?
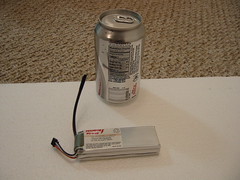
The charger I got is a Hyperion EOS 5i. I have about zero fear of taking things apart so I took a peak inside. It looks well built, the case is all aluminium and the buttons are sealed. There are 2 black heat conduits of a material I can’t identify that connect to the back plate of the charger to what I assume are mofsets (voltage regulators). There is some sort of thermal interface material between the conductor and the back plate. I didn’t want to break the interface in case it is a pad so I didn’t take the back plate off.
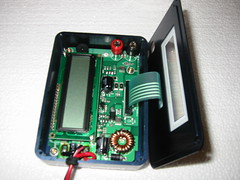
Removable input cables would have been nice. I could have used a different set to connect to a PSU and saved the alligator clips for charging from a field battery. I don’t like alligator clips or bare connectors on a cable, they make me nervous.
Weight Report
I will have a full weight report at the end of the build. The Instructions claim the final weight will be 12oz without the battery. Right now its up to 5.6 ounces. The running gear will add another 5oz so its going to be tight.